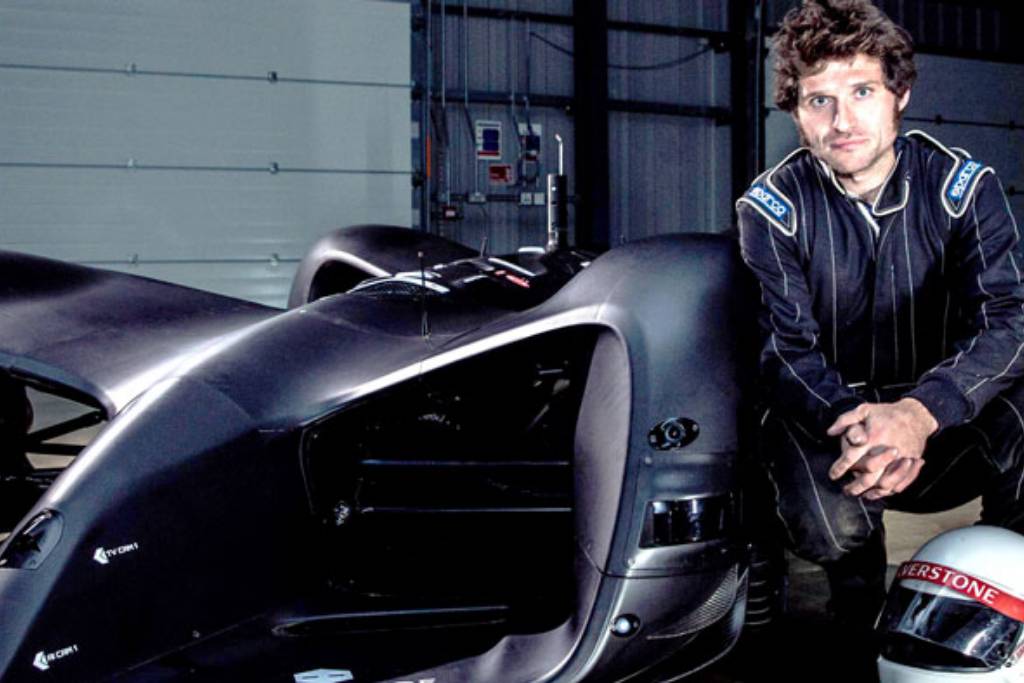
Novatech keeps a foot in both camps as Guy Martin takes on the Robot Car
Novatech products feature on both sides of a contest between Guy Martin's Transit van and the world's most advanced AI racecar.
Force Measurement in Electric and Self Drive Vehicles
Plans to limit the sale of new petrol or diesel engined vehicles are being implemented by a number of European countries over the next few decades. Most of these countries have signed up to some form of environmental policy committed to significantly reducing carbon emissions. Electric powered vehicles are slowly becoming more commonplace but there is a desperate need for improved infrastructure and battery technologies. Without these, the range afforded by a single charge can still be off-putting for many motorists.
The development process of any new technology often requires the precise measurement of key performance parameters to aid in design reviews and final product testing. Loadcells supplied by Novatech are already in use at large automotive companies such as BMW who wish to further their development of electric vehicle technologies and production processes. During development of the i3 and i8 electric vehicles, engineers at BMW found that the batteries they were testing tended to expand as power was drawn. As the batteries expanded they would become less efficient, which resulted in the ECU sensing a reduction in the level of power being supplied. The control unit drew more power from the battery to compensate for the loss but only served to cause further expansion and efficiency losses. Dangerous feedback loops could be created in which the battery would continue to expand until the casing ruptured. Sensors were used to measure the outward force exerted by the battery cases and relay this to the ECU to prevent it from over- stressing the batteries.
Parallel to the development of electric vehicles, a number of companies are in late stage development of 'self drive' cars controlled by artificial intelligence (AI). The AI is linked to a wide array of sensors used to process real-time information about the car's surroundings. This allows the AI to stay on course and react to traffic, road conditions and hazards. Self drive cars hope to greatly reduce the number of fatal road accidents and further improve energy efficiency by driving in a smoother and more controlled manner compared to that of a typical driver. Loadcells can be used both during development and in the final iteration of self drive vehicles to aid with the feedback control system and vehicle dynamics.
Despite significant advancements being made by a number of companies, many people do not like the thought of giving up control to an AI system and would need to see evidence of the systems working in the real world. There is particular concern over how the AI would react in an emergency compared to a human driver. A group of engineers speculated that the best way to engage with the general public would be to combine a detailed technical demonstration with a popular spectator event. In order to showcase the capabilities of their AI software and promote further study in this field, the concept of an exciting new racing series was proposed. The intention was that these races would be contested solely by autonomously controlled electric cars and Roborace Ltd was subsequently incorporated.
Roborace have begun by developing a number of self drive racing cars and have been making these available to other AI development teams. Software engineers could test their systems at events held over Formula E race weekends around the world, with plans for the future being to allow teams to enter their own vehicles in completely AI contested races.
Set-up Wheel Loadcells
As part of the initial development, Roborace have been using a set of Novatech set-up wheel loadcells in order to get their cars track ready. Set-up wheel systems have proved popular with Formula 1 and touring car teams alike and are used to measure various key parameters relating to the dynamics and suspension of the car.
Based on the popular F256 loadcell, set-up wheel loadcells incorporate a ball transfer unit and axial cable outlet for ease of use. A pair of loadcells are mounted at the base of a frame which bolts directly to the wheel hub. With a frame at each corner, the car is raised off the floor and can be moved around the workshop on the ball transfer units. The roller balls also serve as single points of contact, meaning that the load is focused correctly even when the set-up frame is tilted due to the camber angle. This results in the load cell giving less than 0.25% total error for camber angles up to 3° from vertical.
Set-up wheel systems allow Race Engineers to implement changes to ride height, toe and camber angles and make adjustments to weight distribution without continuously raising or lowering the car. Set-up wheel system provide the team with individual corner weights and Mantracourt license free wireless telemetry units relay the measurements from each corner back to a PC or laptop. The dedicated software can be used to calculate the centre of gravity, displaying front/rear and left/right balance. This is extremely useful for any race car set-up and even more important for Roborace who also need to distribute the weight of numerous other sensors around the car in ways that do not impede handling performance. Loadcells were also used as a means of dynamic force feedback for the control system, as the car needed to be programmed to estimate and sense the point at which grip starts to be lost when cornering at high speed. Roborace have experienced some set backs due to the nature of their project but have also enjoyed a lot of success and publicity.
Roborace and Novatech in the Public Eye
Using the chassis of a Ginetta LMP3 car, and completed in the summer of 2016, the first development car 'Devbot 1.0' was tested at Formula E Championship events during the 2016/17 and 2017/18 seasons. During testing ahead of the 2017 Buenos Aires e-Prix, two DevBot cars raced against each other, fully autonomously, reaching top speeds of around 186km/h (116mph). The winning car demonstrated fast AI response and excellent handling in front of crowds of spectators when a stray dog ran on to the track. The unexpected turn of events saw the animal seem to head straight towards the oncomming car. However, the AI was able to react to the situation, adjusting its course and speed to avoid the dog and take another path without crashing or losing control.
The 'Devbot' has since made a TV appearance in November 2018 on a Channel 4 programme Guy Martin vs the Robot Car. In this programme Guy attempted to create the world's fastest driver-less van from a Ford Transit, taking on the Roborace development car around Silverstone. By fitting Anthony Best Dynamics' steering, pedal and gear robots to the van, Guy was able to create his own autonomously controlled vehicle.
Whilst his highly sophisticated competition uses its variety of sensors to learn the track by itself, Guy's van needed to be programmed to map out the layout of the track. Control was implemented through force feedback with loadcells used as an integral part of the Anthony Best Dynamics equipment. Loadcells placed in line with actuators and at the interface with the pedals helped the control system apply the correct forces for smooth control.
The loadcells used by Anthony Best Dynamics in their systems are also supplied by Novatech Measurements, meaning that Novatech were able to proudly keep a foot in both camps as Guy went head to head with the robot car. We are extremely pleased to see our equipment showcased in this way and for similar reasons we have agreed to provided a number of our loadcells to Alto Racing as part of an informal sponsorship deal. These have demonstrated the potential for loadcells to be used to help achieve optimum performance.
Novatech Measurements Proudly Sponsoring Alto Racing
Loadcells from Novatech Measurements are used by a large number of successful racing teams worldwide, including multiple F1 championship winners. However, these loadcells are used extensively for R&D purposes or during pre-race set-up, so there is little visible evidence of our involvement when cameras are rolling. It is for this reason that we are particularly proud of our involvement with the motor bike team of Alto Racing. Our loadcells are highly visible within the frame of the bike and our company logo is prominently displayed on the body.
Using in-line loadcells to measure the inertia during deceleration, the bikes created by Alto Racing actively counteract compression on the front suspension caused when braking for a corner. This is achieved by taking force measurements in real-time and applying equal and opposite force through a pair of actuators. The result is that the bike stays perfectly level even under extremely heavy braking, allowing sharper deceleration without pitching the rider forward. It is even possible to programme a deliberate rise in the front suspension to help the rider stay in the correct position despite the inertia of their own body weight. As a result the rider can maintain more weight over the rear wheel for better grip. This allows the rider to carry considerably more speed into the corners.
The benefit of this force feedback system was found to be so great that riders found it hard to push the machine to its limits. Testing was hampered due to preconceptions as to how a normal bike would handle. To remedy this, a system of coloured lights displayed on the dashboard was created to give the rider a visual cue for when the bike should theoretically start to loose grip. If the test riders were not consistently within a particular zone on the display they were not pushing the bike hard enough and should look to push harder on the next lap. After getting used to the system, riders were consistently able to beat lap records at numerous tracks.
As with many of the revolutionary developments made by Formula 1 teams over the years, the innovative design from Alto Racing was considered so game changing in its effectiveness that the governing body excluded its use from future events in that series. Alto Racing had to look for a different classification in which to compete and for a time even considered creating their own racing series to face all challengers. With their latest bike they now have many wins to their name in a more competitive series and continue to further develop the technology with the aid of Novatech products.